Rotor Spinning Process, Open End Yarn Manufacturing Process
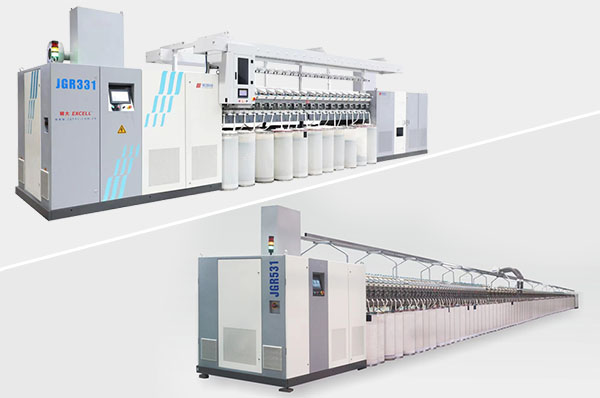
Rotor spinning process
Rotor spinning is the most wide system in the open-end yarn manufacturing industry. It has all the necessary requirements for an efficient spinning method. The open-end spinning has some limitations. It is not suitable for spinning fine count yarn. More bulkiness results in the open end yarn in this process. The high twist multiplier gets employed in this method.
OE Spinning Machine
JGR331 Open End Spinning Machine (OE Spinning Machine) using suction type spinning box, bearing type rotary cup; The whole structure of the equipment adopts flat design to reduce the operation height. The applicable raw materials of the equipment are: pure cotton, pure polyester, polyester cotton, viscose and so on. It has the characteristics of energy saving and high efficiency...
The open end yarn poses good abrasion resistance. This is the special character of open-end yarn getting produced in rotor spinning. The open end yarn consists of wrapped fibres around the yarn surface. The open end yarn also contains a thin outer layer of fibers with hardly any twist or even with twist in the reverse direction. The new fibres get joined on to the already well-twisted fibre strand during each rotation of the rotor. These latecomers receive only a fraction of the desired twist level. If this low twist is lower than the false-twist, the fibres get twisted in the reverse direction.
Open-End Spinning, Open end yarn manufacturing process
The heart of the open-end process is a rotor, wherein fibers can be collected and then drawn off as a yarn. For short staple spinning, most rotors are 31 to 56 millimeters in diameter and may contain a shallow "U" or "V" shaped fiber alignment groove around their eriphery. In openend spinning, the rotor rotation provides the twisting force.
Twist has traditionally been inserted into yarn by rotating the package upon which the yarn is being wound. In the case of open-end spinning, the twisting force is generated by the rotation of a rotor and is transmitted by friction to the fibers that make up the tail of the newly-formed yarn. As this twisting tail comes into contact with other fibers, it collects them. Once this process is started, it is self-sustaining, and yarn can then be drawn out of the rotor continuously. In order to prevent twist from being transmitted throughout the length of the fibers that are available for collection into yarn, it is necessary that these fibers not be in any significant frictional contact with one another. It is from this requirement, that the supply fibers not be in intimate frictional contact, that open-end spinning derives its descriptive name. This lack of contact allows true twist to be inserted into the yarn, and at the same time, prevents twist from being transmitted throughout the fiber supply, which would result in instant stripping of the rotor.
Ring Spinning VS Open-End Spinning Differences:
The basic difference between ring-spun yarns and open-end spun yarns is in the way they are formed. The former produces yarn by inserting twist into a continuous ribbon-like strand of cohesive fibers delivered by the front rolls, while the latter forms yarn from individual fibers directly by collecting them from the inside surface of a rotor by twist forces. Thus, for comparison, it could be said that a ring yarn is formed from the outside in, while open-end yarn is formed from the inside out.